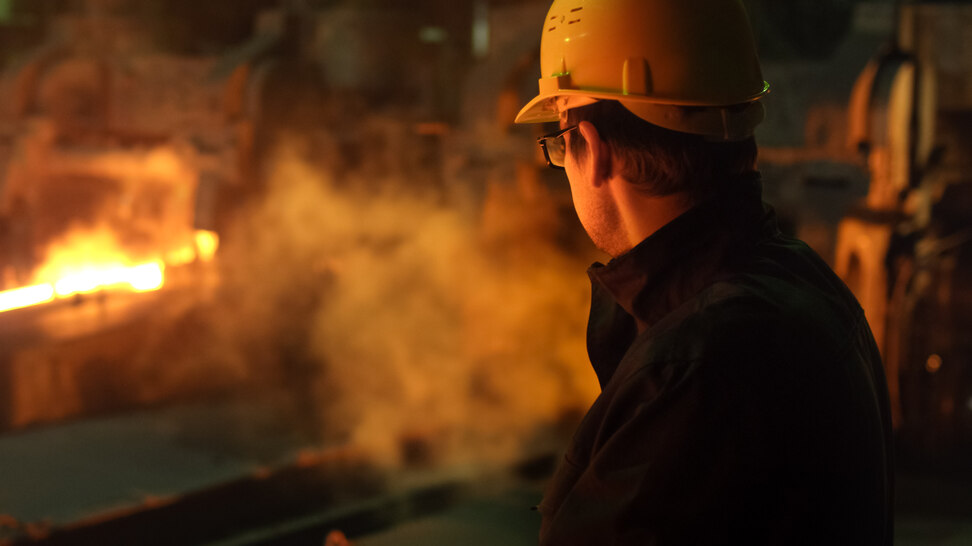
Why is gas analysis important in the glass industry?
There are many economic and technical reasons for a continuous gas analysis in the glass industry. The most frequent reasons include:
- Extending the service life of the furnace
- Safeguarding high and consistent product quality
- Reducing energy consumption
- Ensuring a controlled addition of chemicals
Gas analytics provides a significant contribution to optimizing all operational processes and their monitoring, thus helping to achieve the set goals.
The M&C approach
The procedure in the gas analysis system
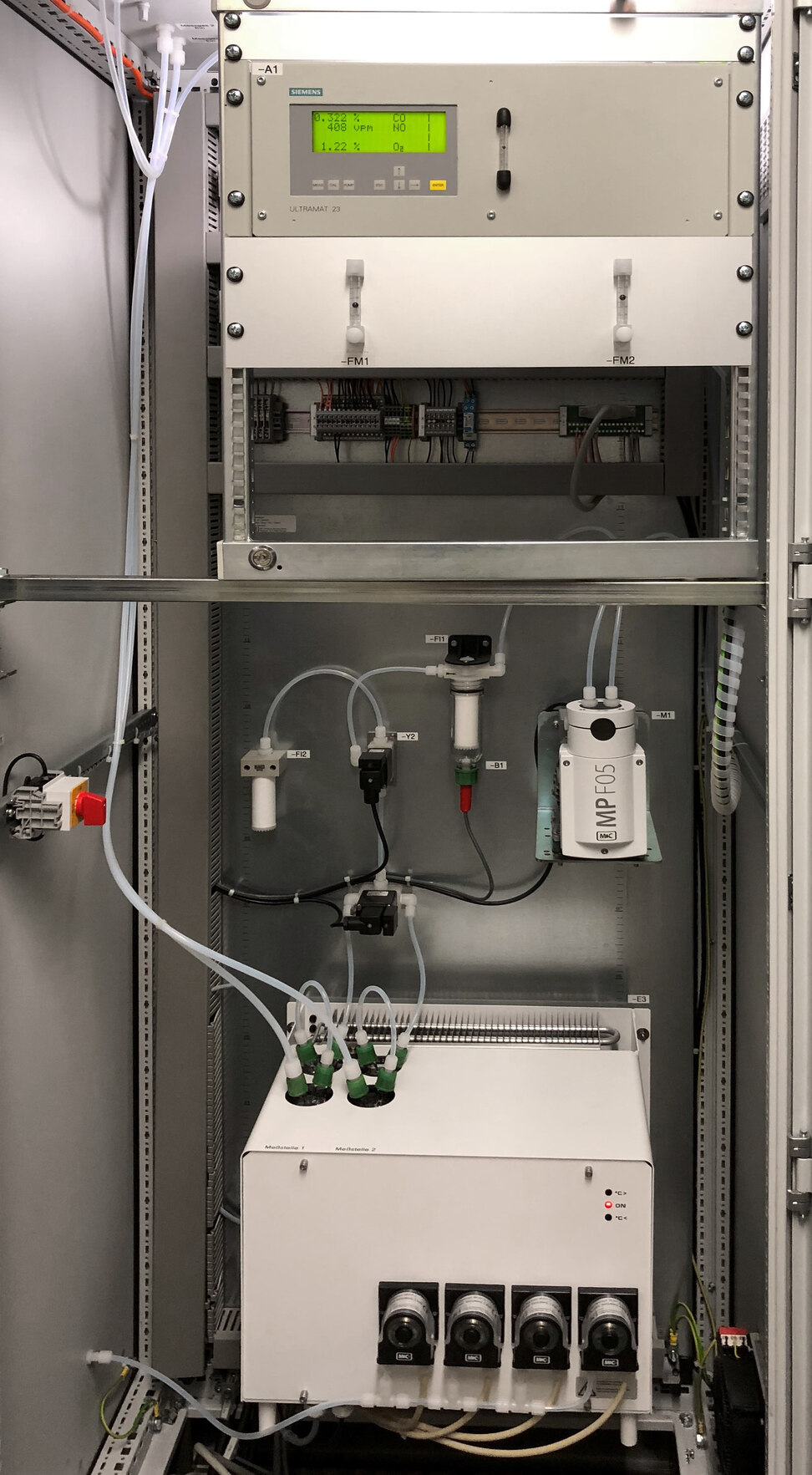
The gas extracted from the measuring points is directed to the gas analysis cabinet via two sample gas lines.
Both sample gas paths are first passed through the Compressor Gas Cooler ECS-4G to dry the sample gas.
The measuring point switchover (MP1/MP2) is performed by a 3/2-Way Solenoid Valve installed in the system.
In addition, the built-in Humidity Sensor LA/LA1.4 is responsible for monitoring the function of the cooler.
In this case, the subsequent filtering of the sample gas is performed by the Universal Filter FP-2T.
For a continuous and reliable sample gas extraction, we integrate the Bellows Pump MP-F05 into the system.
In addition, the Flow Meters FM40 and FM150 ensure continuous flow monitoring by controlling the sample gas flow to the analyzer and the bypass. Through another solenoid valve, ambient air is drawn in via the Ambient Air Suction Filter SP52. The filtered air can then be used as zero gas and provided to the analyzer for its daily adjustment.
Since measurements are carried out alternately at only one measuring point at a time, the system requires only one gas analyzer for measuring CO, NO and O2.